Know About Wear
Wear is the deterioration of a component causes due to the friction of
material, slag, cement, and so forth. Plant machinery and components mainly
get affected and the result is huge losses and expensive maintenance cost.
To combat these losses, we provide Wear Resistant Lining Solution ideal for
various industries like coal, power plants, food, cement, fertilizer,
mining, and others. We have robust manufacturing plant to develop Wear
Resistance Ceramics with improved features that help in Abrasion Resistant
Lining of plant components such as coal mill equipment, ash handling bends,
grinding media, scrapper conveyor, and others. Wear Solutions offered by us
reduce the maintenance cost and improve productivity.
««« Following are the Causes of Wear »»»
Cement
Industries
|
Mineral
Processing Industries |
|
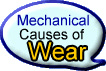 |
FRICTION : Rubbing between two
surfaces |
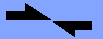 |
ABRASION : Removal of particles |
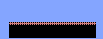 |
IMPACT : Cracks and Breaks |
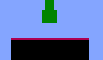 |
HEAT : Reduction of
hardness |
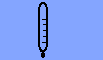 |
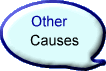 |
CHEMICAL : Deterioration of
microscopic structure |
 |
|
 |
««« Ceramics »»»
Alumina Ceramics
Guidelines by BMW Steels Ltd. for WEAR RESISTANCE
Alumina |
SLIDING |
FRICTION |
ABRASION |
IMPACT** |
HEAT |
CHEMICAL |
Sintered Alumina Ceramic |
Very High |
Low coefficient |
25 - 30 times* |
Medium** |
1000 °C |
High |
*In Comparison with Mild Steel: 1
time |
**ANGLE OF INCIDENCE
- maximum recommendable - depending on particle size of product
being worn |
Guidelines by BMW Steels Ltd. for WEAR
RESISTANCE for guidance only, having been produced -
after selection of the product most appropriate to ORIGIN OF WEAR:
Abrasion, Impact, Heat, Chemical, etc.- from data obtained on
visits to Factories. |
|
 |
HARDNESS |
ANALYSIS |
DENSITY |
COLOUR |
09 MOH |
Al 2O3 90 % |
Min. 3.6 gm/cm3 |
White |
Thickness minimum 4 mm. for mortar fixed and 10 mm for weldon tiles.
Basalt
Guidelines by BMW Steels Ltd. for WEAR RESISTANCE
Basalt |
SLIDING |
FRICTION |
ABRASION |
IMPACT** |
HEAT |
CHEMICAL |
Cast Basalt |
High |
Low coefficient |
15 - 20 times* |
Low** |
350 °C |
High |
*In Comparison with Mild Steel: 1
time |
**ANGLE OF INCIDENCE
- maximum recommendable - depending on particle size of product
being worn |
Guidelines by BMW Steels Ltd. for WEAR
RESISTANCE for guidance only, having been produced -
after selection of the product most appropriate to ORIGIN OF WEAR:
Abrasion, Impact, Heat, Chemical, etc.- from data obtained on
visits to Factories. |
|
 |
HARDNESS |
ANALYSIS (%) |
DENSITY |
Al2O3 |
SiO2 |
Fe2O3 / FeO |
CaO |
MgO |
K2O |
Na2O |
TiO2 |
8 MOH |
14 |
50 |
12 |
12 |
10 |
4 |
4 |
3 |
3 gm/cm³ |
Thickness minimum 20 mm.
CBC
Guidelines by BMW Steels Ltd. for WEAR RESISTANCE
CBC |
SLIDING |
FRICTION |
ABRASION |
IMPACT** |
HEAT |
CHEMICAL |
Chemically Bonded Ceramics |
Very High |
Low coefficient |
15 - 20 times* |
Medium** |
1200 °C |
High** |
*In Comparison with Mild Steel: 1
time
*** for chlorides & sulphides |
**ANGLE OF INCIDENCE
- maximum recommendable - depending on particle size of product
being worn |
Guidelines by BMW Steels Ltd. for WEAR
RESISTANCE for guidance only, having been produced -
after selection of the product most appropriate to ORIGIN OF WEAR:
Abrasion, Impact, Heat, Chemical, etc.- from data obtained on
visits to Factories. |
|
 |
HARDNESS |
Compressive Strength |
DENSITY |
Fraction Energy |
07 - 08 MOH |
1200 Kg / cm² |
2.5 - 2.9 gm / cm³ |
15,000 J / m² |
Thickness minimum 20 mm.
««« Alloyed Iron »»»
Chrome Steel
Guidelines by BMW Steels Ltd. for WEAR RESISTANCE
Chrome Steel |
SLIDING |
FRICTION |
ABRASION |
IMPACT** |
HEAT |
CHEMICAL |
as per IS 4896 |
Low |
Low coefficient |
4 - 6 times* |
High** |
Low
200 °C |
Low |
*In Comparison with Mild Steel: 1
time |
**ANGLE OF INCIDENCE
- maximum recommendable -
depending on particle size of product being worn |
Guidelines by BMW Steels Ltd. for WEAR
RESISTANCE for guidance only, having been produced -
after selection of the product most appropriate to ORIGIN OF WEAR:
Abrasion, Impact, Heat, Chemical, etc.- from data obtained on
visits to Factories. |
|
 |
HARDNESS |
ANALYSIS (%) |
DENSITY |
C |
Si |
Mn |
S |
P |
Ni |
Cr |
V |
Ti |
350 BHN |
0.45 - 0.65 |
0.75 MAX |
0.5 - 1 |
0.06 |
0.06 |
TRACES |
0.8 - 1.5 |
- |
- |
7.8 gm/cm³ |
Thickness minimum 16 mm.
««« Un-Alloyed Iron »»»
Cast Iron
Guidelines by BMW Steels Ltd. for WEAR RESISTANCE
Cast Iron |
SLIDING |
FRICTION |
ABRASION |
IMPACT** |
HEAT |
CHEMICAL |
as per ASTM-A48 Class 20-60 |
High |
Low coefficient |
0.9 to 1 times* |
High ** |
Medium
500 °C |
- |
*In Comparison with Mild Steel: 1
time |
**ANGLE OF INCIDENCE
- maximum recommendable - depending on particle size of product
being worn |
Guidelines by BMW Steels Ltd. for WEAR
RESISTANCE for guidance only, having been produced -
after selection of the product most appropriate to ORIGIN OF WEAR:
Abrasion, Impact, Heat, Chemical, etc.- from data obtained on
visits to Factories. |
|
 |
HARDNESS |
ANALYSIS (%) |
DENSITY |
C |
Si |
Mn |
S |
P |
Ni |
Cr |
V |
Ti |
180 BHN |
0.3 MAX |
0.75 MAX |
0.5 - 1.5 |
0.06 |
0.06 |
TRACES |
TRACES |
- |
- |
7.8 gm/cm³ |
Thickness minimum 12 mm.
Ni-Hard
Guidelines by BMW Steels Ltd. for WEAR RESISTANCE
Ni-Hard |
SLIDING |
FRICTION |
ABRASION |
IMPACT** |
HEAT |
CHEMICAL |
as per IS 4771 |
Medium |
Low coefficient |
10 - 12 times* |
Medium** |
550 °C |
- |
*In Comparison with Mild Steel: 1
time |
**ANGLE OF INCIDENCE
- maximum recommendable - depending on particle size of product
being worn |
Guidelines by BMW Steels Ltd. for WEAR
RESISTANCE for guidance only, having been produced -
after selection of the product most appropriate to ORIGIN OF WEAR:
Abrasion, Impact, Heat, Chemical, etc.- from data obtained on
visits to Factories. |
|
 |
HARDNESS |
ANALYSIS (%) |
DENSITY |
C |
Si |
Mn |
S |
P |
Ni |
Cr |
Mo |
Ti |
550 BHN |
2.7 - 3.3 |
1.5 - 2.2 |
0.3 - 0.6 |
0.15 MAX |
0.3 MAX |
4 - 6 |
8 - 10 |
0.5 MAX |
- |
7.9 gm/cm³ |
Thickness minimum 20 mm.